How to use a compression router bits with your CNC router machine?
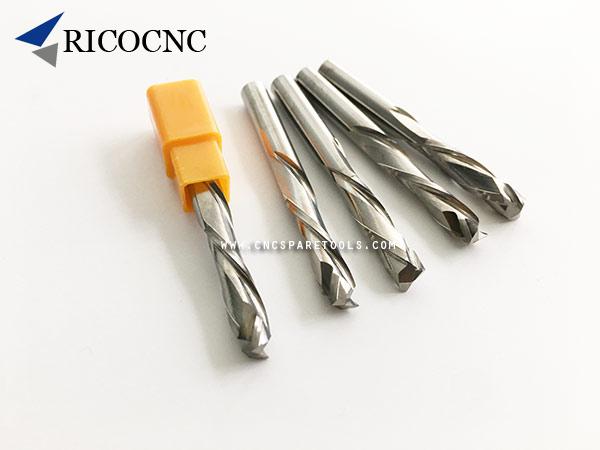
How to use a compression router bit?
CNC router machines need bits. There are a lot of kinds of router bits for different purpose. Different type
router bits, different usage. They determine the kind of processing you can do, the resolution of your finished designs, and how fast you can move through the material.
What is a compression bit?
A compression bit is the combination of both upcut and downcut spirals. Typically, a compression spiral has an upcut single, double or triple flute at the tip of the cutter, approximately one third of the cutting length. The remaining two thirds is ground to give a downcutting shear.
By combining both geometries, you achieve a win/win situation. The bottom of the material is pulled upwards while the top of the material is pushed downwards thus eliminating the risk of damaging the laminated surfaces. When run at full depth, the bit leaves a sharp, clean edge on both sides of your workpiece.
A compression bit can be a little more expensive than standard router bits, however
RicoCNC recommend them as an essential tool when processing double laminate wood materials.
Why use this over a conventional upcut or downcut bit?
Compression bits are used extensively for cutting double side laminates such as melamine or plywood. These tools can also be used on natural woods where edge finishing is a problem with standard spiral tools.
A dedicated up or downward spiral may only give a good finish on one side of the material if the material is laminated. Where both sides of the material require the best possible finish, a compression bit is your best solution.
How do I use this tool correctly?
While compression bits are the tool of choice for cutting double side laminates, it’s essential you use the tool correctly.
The cutting edge of most tools are on the side of the tool, therefore a direct plunge into the material will be fine for your standard upwards tool as the waste material is lifted out of the cut line and into the extraction system.
However, for downward spirals and/or compression tools, it is best to ramp into the material. This approach stops the swarf from compressing at the bottom of the tool and causing extreme levels of heat. This heat will damage the cutting edge of the tool and the work piece.
For those who are unaware of the difference between plunging and ramping, it can be explained below:
Plunge: A vertical Z movement directly into the material.
Ramp: While the tool is driving into the material, it is also moving forward along the programmed path.
RicoCNC supplies all your
router bits,
spare parts and consumables, we are a one-stop shop for everything CNC.
Welcome your inquiry,
Contact us NOW.